Yutwin
Product Overview
Casting nozzle material is a part of the feeding component of double-roll aluminum strip billet continuous casting mill. Through casting nozzle material, aluminum liquid is reasonably and uniformly fed into the casting roll seam, and then through the casting rolls, the semi-solid aluminum liquid is cooled and pressurized to output the aluminum slab blanks. The performance index of casting nozzle material plays a key role in the quality of aluminum slab blanks. The casting nozzle material is made of inorganic ceramic material, with stable performance, not easy to deform, not bonded, not infiltrated with molten metal aluminum, which can completely guarantee the continuous and stable output of aluminum slab blanks.
* Performance requirements may result in changes in chemical composition. Test Criteria
Typical Chemical Composition
Ai₂O₃ | SiO₂ | Fe₂O₃ | Inspection Standards Different |
27-34 | 65-72 | 0.2-0.3 | GB |
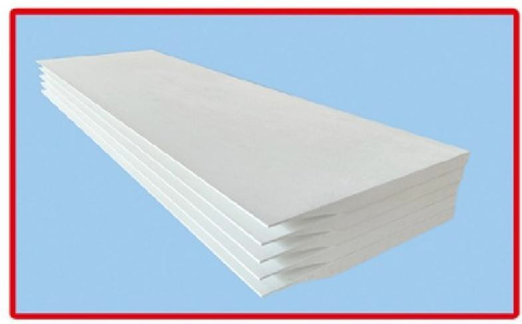
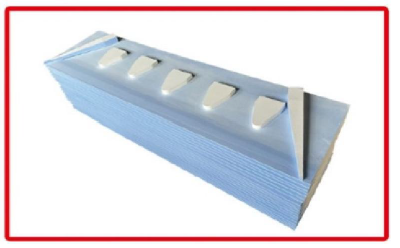
Bulk density g/cm3 | Line shrink age% 700℃×3h | Thermal conductivity 700℃W/m.K | Compres sive strength Mpa | Flexural strength Mpa | Water content % |
0.42-0.6 | +0.1 | ≤0.1 | ≤3 |
Storage and transportation
Dry storage, placed in a ventilated dry place, is strictly prohibited in wet places, rain, and moisture.
Wooden packaging: the product is fragile and properly stored. Prevent extrusion and impact during transportation.
How to use the product
1. According to the production process requirements of sizing, cutting, assembling and fixing.
2. The cast nozzle material needs to be dried before use, normal drying system: 170-240 ℃, holding time ≥ 4 hours.
Other Precautions
1. The material should be put into use as soon as possible after assembling and baking to prevent secondary moisture absorption.。
2. In humid season or after stopping because of the high temperature of the roll surface, the roll surface is easy to bead up; it is recommended to bake with the flame of the baking roll for 10-15 minutes at the exit side of the roll and then set up the plate.
3. If the casting material is improperly stored and soaked by rainwater, do not put it into use even if it is dried.
Product Overview→Degassing and Filtration Chamber
Aluminum liquid on-line degassing and filtration equipment is the most important equipment in the process of aluminum liquid melting and purification, which is the basic guarantee for deep processing of aluminum alloy, and its function is to remove hydrogen and harmful impurities in aluminum liquid. When the liquid aluminum passes through the degassing box, the rotor (or permeable brick) rotating in the degassing
box removes the hydrogen and slag in the liquid aluminum,
and is heated and kept warm by the heater in the degassing box. Through the filtration box, the aluminum liquid is
purified and filtered for the second time by the filter
sheet (or filter tube and other filters and filter media), so that the quality of the aluminum liquid meets or
exceeds the production requirements and lays the foundation for the deep processing of subsequent products.
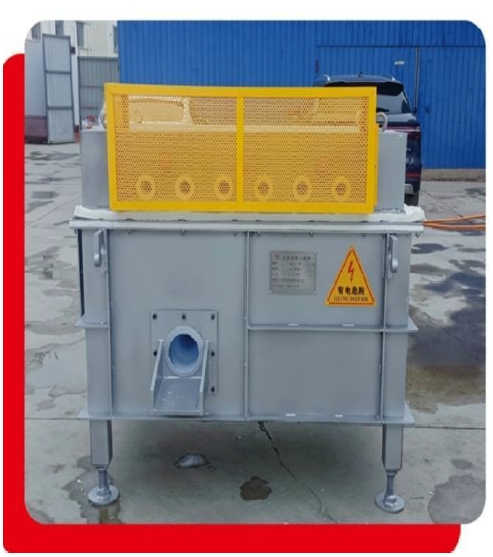
Main structure of degassing box and filtering box
Box type | General box structure | Commonly used degassing and deslagging methods | Use features |
Degassing box | Single chamber, double chamber | Rotor type degassing | High degassing efficiency |
Vented brick type degassing or combined with rotor | Convenient and economical | ||
Filter box | Single channel single-double-layer Double-channel single-double-layer | Filter sheet type | High productivity in a wide range of applications |
Tube filter type | Precise and reliable operation | ||
Tubular filter box Deep-bed filter box | Particle layer filter type | High filtration accuracy |
Typical Parameters and Options
Case Aluminum Liquid Handling Capacity | Case Wall Temperature Rise | Degassing Rotor Material | Speed Adjustment | Lid Lifting Method | |
5t/h | ≤50℃ | Graphite/Sil icon Carbide | Frequency converter | Mechanical Hydraulic | |
Heating power | Heating control ler type | Heating mode | Equipment control mode | ||
20–40kw | Silicon Controlle d | Immersion | Instrumenta tion, PID/touch screen, PLC |
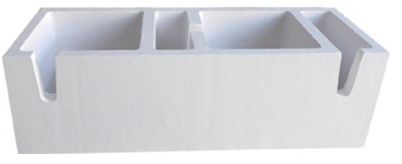
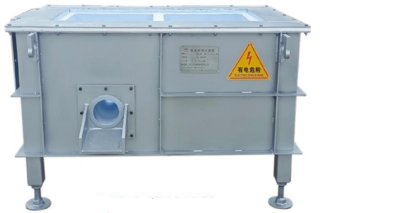
Commonly used filter size | Temperature rise of the outer wall of the case | Filter material | Heater control method | Lid Lifting Method | |
12/15/17/20/23in ch 305/381/432/508/58 4mm | ≤50℃ | Aluminum- silic on ceram ics | Instrumenta tion, PID/touch screens, PLCs | Mechani cal / Pneumat ic / Hydraul ic. | |
Heating power | Heating controlle r type | Heating method. | |||
30-50kw | Silicon Controlled | Radiant. |
Usage and Precautions
1. Before using for the first time, be sure to follow the baking curve to raise the temperature of the
baking.
2. Strictly prohibit open flame flame direct contact with the furnace wall, baking temperature should
not exceed the maximum operating temperature of the box.
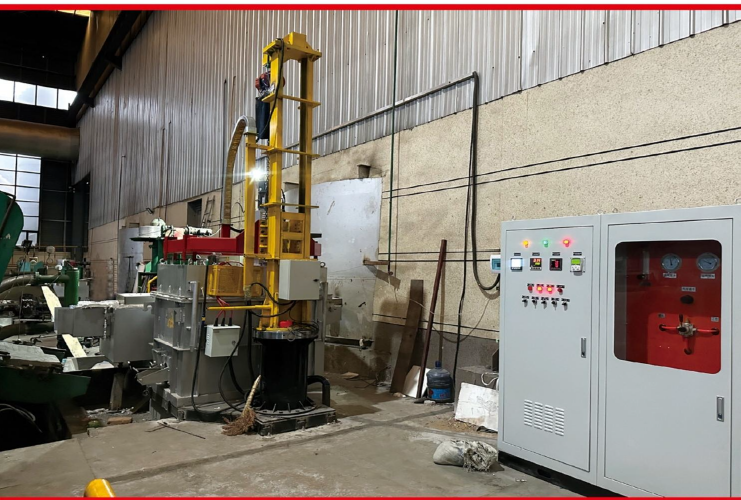
Main technical parameters
Gas source requirements
1. Working gas: industrial nitrogen, argon or mixed gas
2. Gas pressure adjustment range: 0- 0.8Mpa. 8Mpa
3. Gas flow: 0.25-2.5 M3/H
4. Nitrogen Purity:99.9 95%
Comprehensive degassing effect
- Inlet hydrogen content 0.30cm3/100gAL 30cm3/100gAL. Degassing effect: 40 – 50%
- Inlet hydrogen content <0.24cm3/100gAL 24cm3/100gAL Hydrogen content <0 . 12cm3/100gAL 12cm3/100gAL
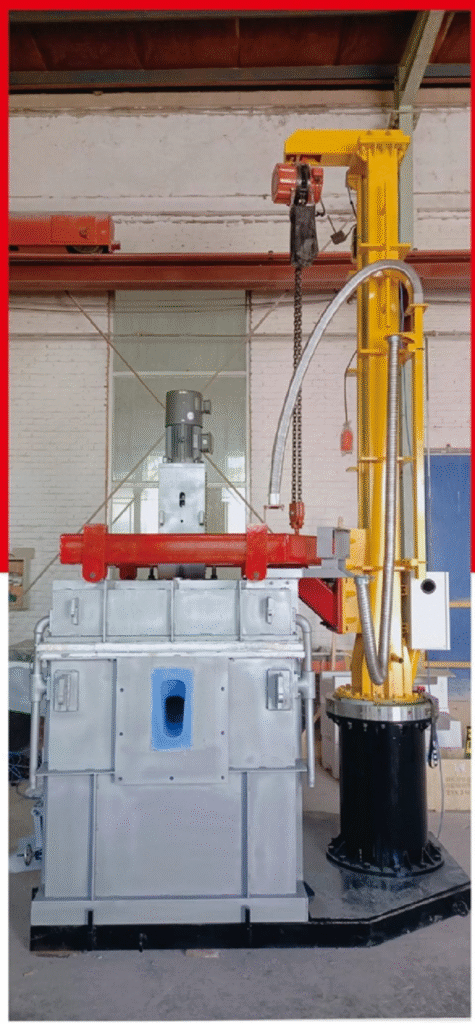
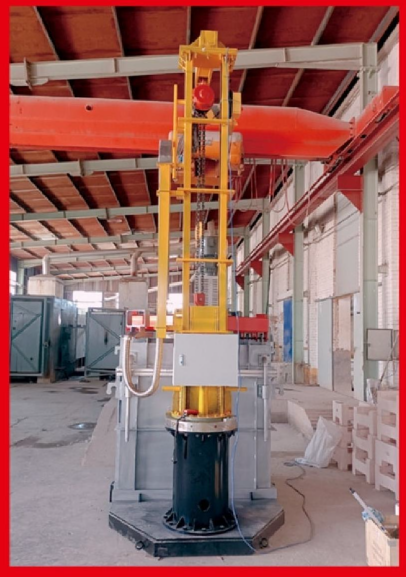
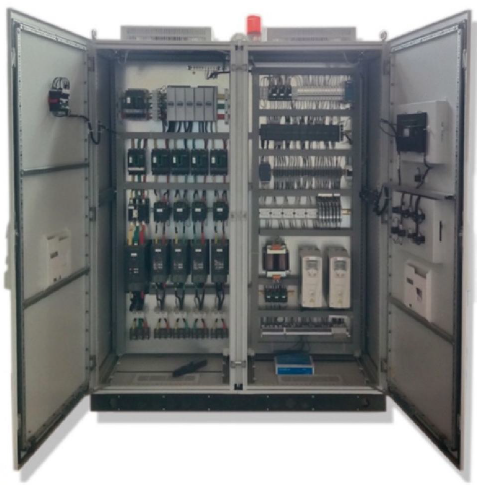
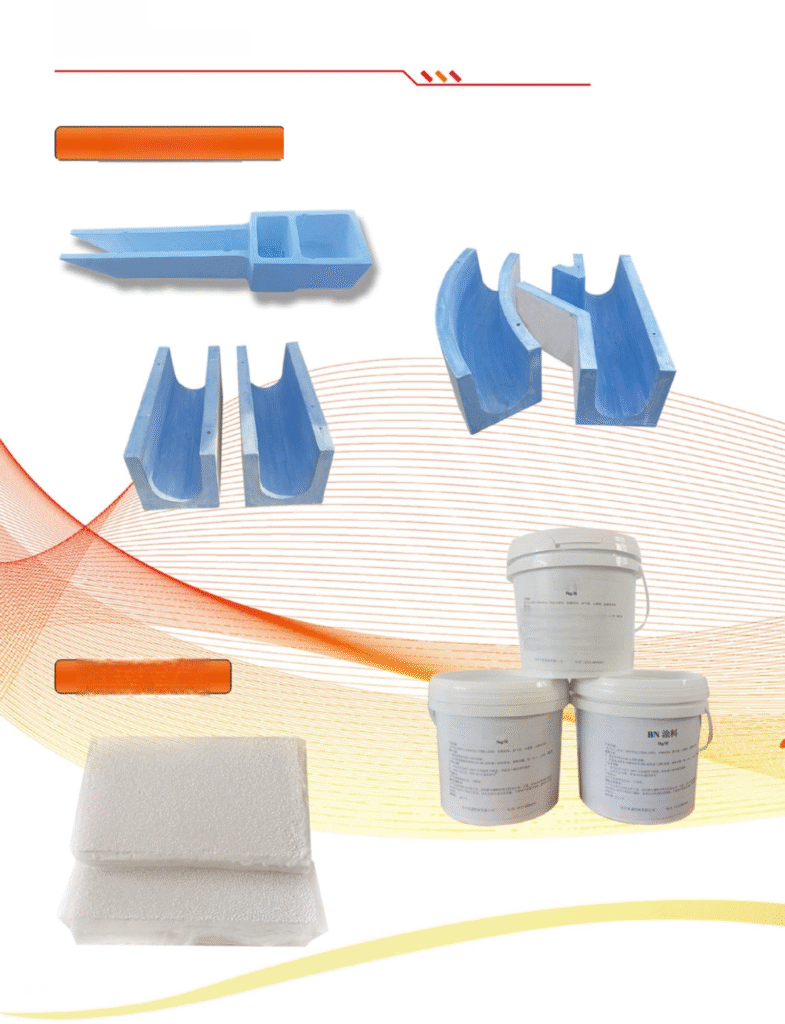
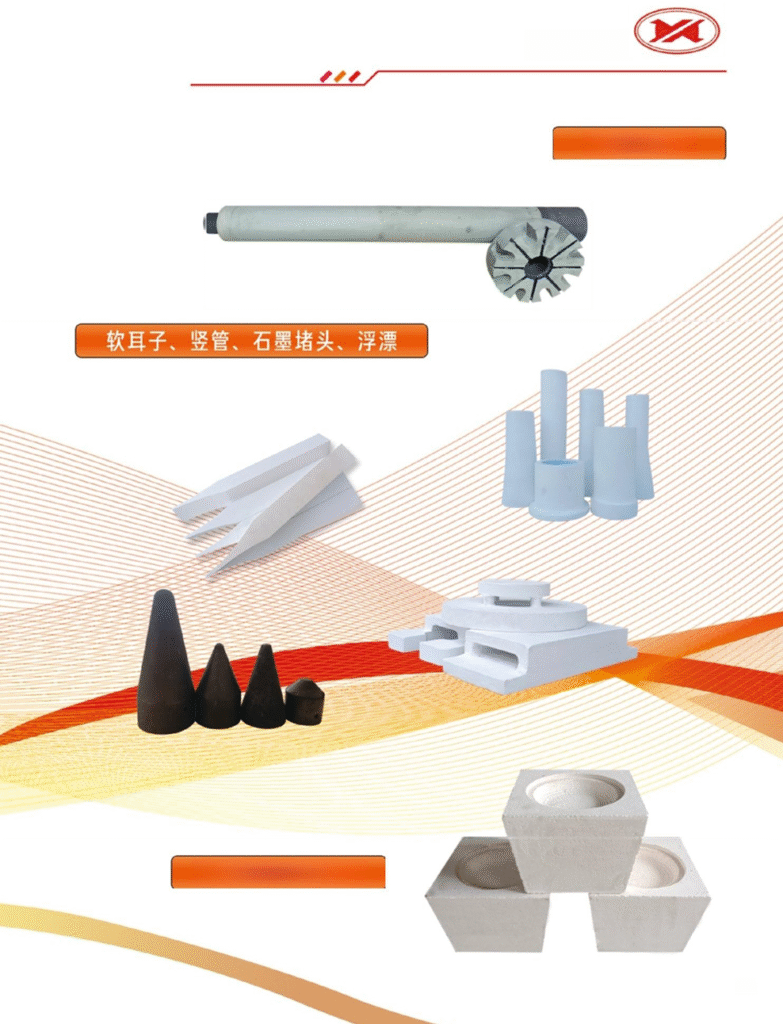
Product Overview
Aluminum flow channels and profiles are essential equipment in the aluminum smelting process, and their technical requirements have a significant impact on the efficiency of aluminum smelting and product quality. The flow channel itself needs to be characterized by high strength, resistance to scouring, not easy to crack and long service life. Our company produces two types of products to meet the above demands. First, we offer lightweight material flow channels, shaped parts, and product density control in the range of 0.8-1.0 g/cm³, featuring lightweight insulation, ease of replacement, and easy use. Lightweight and heat-preserving, easy to replace, use, and process, making it convenient for on-site use. The material of the runner is composed of high alumina, semi-silica, silica, or silicon carbide, depending on the application, and is sintered at high temperatures. The product is resistant to aluminum liquid erosion and does not stick to aluminum. Stable performance, high
strength and long service life. Easy to maintain.
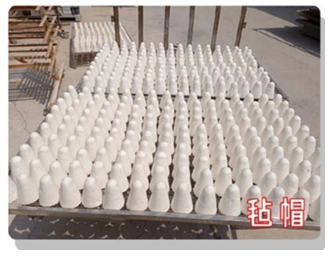
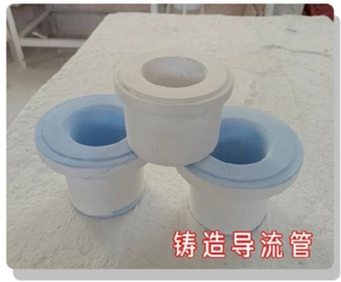
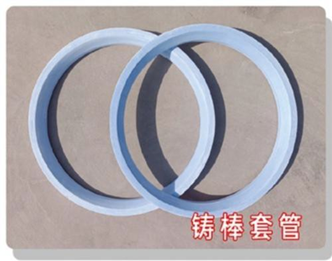